半导体封装超声波压焊的工艺参数优化朱正宇,胡巧声
(1、快捷半导体(苏州)有限公司,江苏苏州 215021;2、上海同济大学机械工程学院,上海 201804)
1 引言 .
超声波焊接另称"键合"是利用超声频率(16~120 kHz)的机械振动能量,连接同种或异种金属、半导体、塑料及陶瓷等的一种特殊的焊接方法。超声波焊接现已广泛地应用于集成电路、电容器、超高压变压器屏蔽构件、微电机、电子元器件及电池、塑料零件的封装等生产中。与传统的焊接技术相比,超声波焊接技术具有高速、高效和高自自动化等优点,成为半导体封装内互联的基本技术。
2 超声波压焊的基本原理
超声波能是机械的振动能,工作频率超过声波(正常的人类听力,其频率上限为18 kHz)。半导体封装所用的超声波压焊的频率一般是40 kHz到120 kHz。超声波压焊是一种固相焊接方法,这种特殊的固相焊接方法可简单地描述为:在焊接开始时,金属材料在摩擦力作用下发生了强烈的塑性流动,为纯净金属表面之间的接触创造了条件。而接头区的温升以及高频振动,则又进一步造成了金属晶格上原子的受激活状态。因此,当有共价健性质的金属原子互相接近到以纳米计的距离时。就有可能通过公共电子形成了原子间的电子桥,即实现了所谓金属"键合"过程。经过对焊接过程的研究表明,摩擦、塑性流动以及温度是实现超声焊接的3个互为依赖的主要因素,其中摩擦起主导作用,这不仅是焊接中的主热源,而且通过排除氧化膜为纯净金属表面间接触创造了条件。
超声焊接摩擦所需能量可由下式表示:
E=∫μPvdt[5]
式中:μ-摩擦系数;P-焊头上所加的垂直压力;v-焊头振速;其中:v=4Af
式中:A-焊头的振幅;f-超声振动频率;t-焊接时间。
在生产实际的超声波压焊的参数中,由于摩擦系数是由焊接材料与焊头和焊件与表面状态、焊件夹持的方法等有关,可以视为常数,压力P与被焊材抖的可流动性极限有关,还与焊件材料的硬度、厚度及焊头振幅大小有关;通常由bonding force来表示,由机器提供的气动压力来控制,所以易于精确调整。振幅是由放大器(变幅杆)和焊接工具的设计所选定,它可由电能的供给自动精确地控制和调整,以能量bonding power来表示,一旦焊接头变幅杆的几何尺寸已定,则固有的共振频率即确定,因此,频率往往在机器设计时就固定已知了,焊接时间由bonding time来表示,可由电气方面精确控制。故:超声焊接摩擦所需能量又可写为:9 u1 r% {0 ]6 u$ }
E=μf∫PAdt
所以有3个基本过程变量:振幅(能量)、压力(力)和时间。因为整个过程所要达到的最终目标是通过供给足够的能量去分裂和分散氧化物,使之在原子距离内彼此形成相对的层面,所以这些变量都是与能量紧密相关。此外,在实际的半导体封装制造过程中,往往采用辅助加热的方法来促进塑性变形,而控制温度的方法是比较简单的,因此,温度也常作为一个过程变量来加以控制。
实际上,在半导体封装领域内的超声波压焊工艺,往往分为热超声和冷超声焊两大类,所谓热超声焊,往往是需要采用加热的方式,通过加热块对工件进行加热,所以焊接温度往往成为需要控制的工艺参数。此外,该工艺需要对焊接金属丝(主要是金线)末端通过火花放电和表面张力作用预先烧制成球,故又成为金丝球压焊,所以对放电电流、时间和距离的控制也是要求比较高的。该工艺往往大量运用于大规模、超大规模集成电路的内互联,是一种比较成熟的工艺,具体工艺过程如图1。
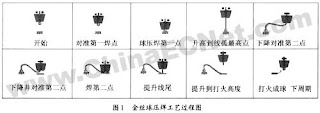
另外一种冷超声焊工艺无需加热方式,焊接工具直接作用于芯片表面,因此所需摩擦能量比较大,焊机也比较大,所焊金属丝也比较粗。此外,该工艺和金丝球压焊工艺的主要区别除了温度以外,还体现在焊接工具上,一般而言,金丝球压焊的焊接工具是主要以陶瓷为基材的毛细管,而冷超声焊通常是焊接铝丝,所以其焊接工具是由钨钢制成,类似锲子,俗称劈刀,有时劈刀可以是两种焊接工具的统称。该工艺主要应用于功率器件和高可靠性要求的半导体器件的内互联,冷超声焊的具体工艺如图2
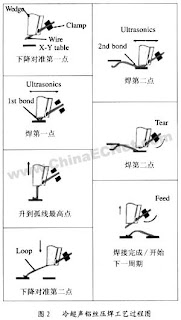
3 超声波焊接工艺的质量要求
判断一个焊点是否满足焊接质量要求的标准往往是通过破坏性实验来获得焊点的强度,通常的拉力测试方法我们称为BPT(Bond Pull Test),有时也参考推力试验,称为BST(Bond Share Test)。通常来说要求焊接强度越大越好,但也受材料的强度极限限制。此外,对于直接作用在芯片表面的焊点来说,除了考虑焊接强度外,还要检查芯片的内部结构是否受损。一般来说,考证焊接强度的质量指标是焊线拉断力的大小,检查芯片内部结构状况的方法使用饱和的强碱溶液来腐蚀掉焊点及芯片表面的铝层,在足够倍率的显微镜下观察内部结构是否受损(cratering),这种测试方法称为Etching
4 超声波压焊的工艺优化方法
在明确了要达到的质量要求后,可以通过试验设计的方法来获得比较优化的焊接参数,来满足要求。一般说来作为一个产品的工艺开发过程涉及的方面是比较多的,除了焊接设备本身,还要考虑焊接材料,在比较成熟的半导体封装厂家,可以认为,这些因素是稳定的。在设备和材料不稳定的情况下,参数优化是没有意义,所得结果也不可靠。在这些条件满足的前提下,我们可以尝试采用试验设计[6]DOE(Design of Experiment)的方法来优化工艺条件。以下举实例来说明优化方法。
要开发一种在MOSFET[2]上打50.8μm铝线的工艺,该工艺的难度是,由于芯片制造的原因,栅极(gate)的焊接区域是限定的,50.8μm铝线采用冷超声,很容易发生焊接脱落的问题,为了防止脱落,须增大焊接参数,主要是能量,但又会产生根裂问题[5],要求优化参数来满足焊接强度要求,并减少根裂的发生可能,同时保证结构不受损。首先需要做的是找到一个大体的参数范围,该范围必须保证没有根裂的情况产生,然后在这个基础上尽量提高焊接强度。针对根裂问题,可提出理想焊点形状要求,一般来说若焊点的厚度在25.4μm以上,就可保证有效防止根裂产生,理论上可通过有限元法来计算证明[5]。寻找参数范围的一般做法是,根据经验,先选择几个比较敏感的参量,做若干组相应的实验以得到相应的响应做拟合分析。需要指出的是所谓根据经验是建立在前人试验和探索的结果基础上,对于一些新产品,新工艺如果没有经验可借鉴,往往要做的是采用筛选试验(screen design)的方法来筛选主要因素和贡献率较大的因素。本例,由于wire bond工艺本身是一个比较成熟的工艺,因此,参数的敏感性和重要性的排列,在业界已有共识[3]。本例采用Orthodyne M360系列的全自动焊机,比较全面地介绍了因素的设计重要性排列和最终的优化结果。
(1)因子设计及初始参数(见表1)。
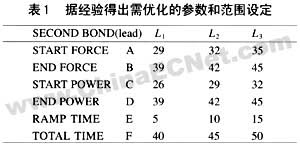
(2)响应设计
我们关心的是焊接强度和焊点的形状,因此在每次试验后,需要做破坏性测试和测量几何尺寸。
采用Dage公司的全自动测试设备,方法如图3,图4所示:
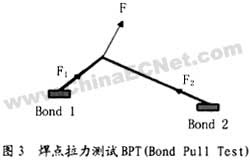
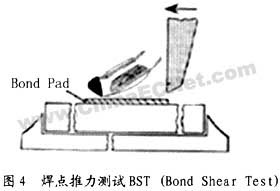
几何尺寸的测量如图5。
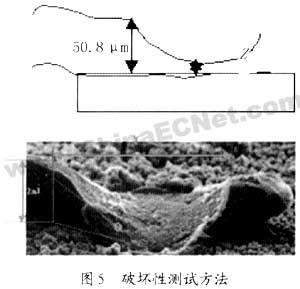
tgθ=(2×25.4-Z)/(y/2)
我们希望在保证焊接强度的情况下,焊点的厚度越厚越好,并同时确保没有打裂芯片。
(3)实验方案设计
在明确了试验的输入(因子)和输出(响应)后,需要设计试验的方案,如果试验次数太少,则所得结果和数据不足以信服地说明问题,如果试验次数太多,则又没有足够资源,例如受到试验材料,设备占用时间,测量设备占用时间等的限制。采用数理统计的方法可以有效地减少试验次数,同时所得数据又足以反映过程实际。我们采用JMP统计软件来运行出试验方案,充分考虑到因子的分布均匀性要求,结果见表2。
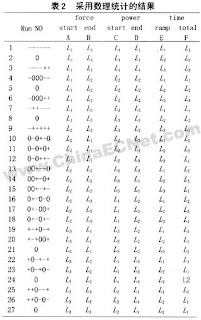
(4)试验结果和论证检验。
由于本例是多因子多响应的情况,所以为了得到比较客观的结果,需要做数据处理,我们对不同的响应设置了不同的权重比例,并采用百分制进行优劣判断。具体结果如表3:(所有的实验都通过了etching检验,确认没有对芯片产生任何损伤和打裂现象,所以可以在数据分析时不考虑这一特性检查。)
采用统计分析软件对响应结果进行分析,得到如下结果:
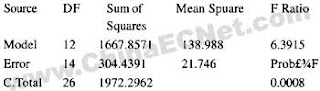
方差分析:
结果表明各因素间对响应有明显的贡献率差异。
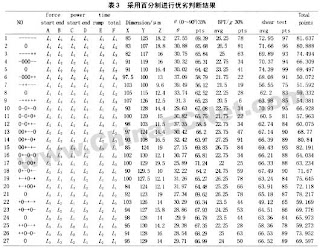
重要性分析如图6所示。
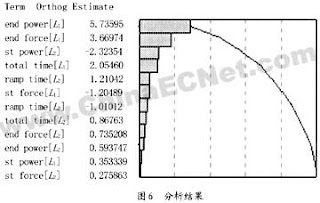
结果表明最重要的因素是end power,和end force,start power和total time也对响应有比较大的贡献率
级差分析见图7。
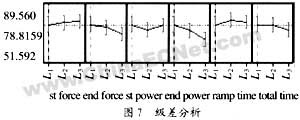
由此可以得出比较优化的参数(见表4)。
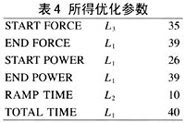
(5)试验结果论证见图8。
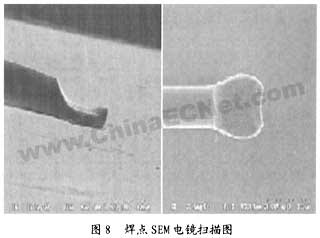
焊点的形状均匀,焊点厚度达到25.4μm以上(如图6所示),对比优化前焊点厚度只有12.7μm大幅度提高了焊点的抗裂性能,同时破坏性测试结果也表明满足焊接强度的要求,因此可以说问题得到了比较满意的解决。
结束语
以上实例详细介绍了超声波铝线焊接工艺参数优化来解决问题的过程,需要重点提出讨 论的是,确定优化的目标往往是问题得以解决的关键,像本例通过力学分析和有限元计算得出减少应力集中的关键是需要控制焊点的厚度和焊线的角度,并通过研究及设备的运动过程和参数控制效果来得出优化结果。实际上针对半导体封装的其它工艺的优化大多是类似的,采用优化办法来稳定工艺,可提高质量和制造水平。如果要开发金线wire bonding工艺,一般来说只要考虑温度、压力、能量和时间4个因素,只要九组试验就可以得到结果,相对本文所举的例子来说更为简单。
本文摘自《电子工业专用设备》
没有评论:
发表评论